InPro-MMS: Intelligente Prozessauslegung zur schmierstoffmengenoptimierten MMS Bearbeitung / Teilprojekt
02/2013 - 12/2013
Prof. Dr. Michael Schneeweiß (Fakultät Automobil- und Maschinenbau)
WHZ-Forschungsprojekt
Prof. Dr. Michael Schneeweiß
+49 (375) 536 1720
michael.schneeweissfh-zwickaude
Prof. Dr.-Ing. J. Vogel (KFT);
Prof. Dr. rer. nat. habil. A. Neidhardt (PTI);
Kennametal Shared Services GmbH
SMWK
Situation
Das visionäre Ziel der „Trockenlegung aller mechanischen Fertigungen von Klein- und Grossserienfertigern“, kann nur durch das stete Ringen um weitere Kühlschmierstoff-mengenreduktionen erreicht werden. Ein wesentlicher Beitrag hierzu, soll durch die Ermittlung der bedarfsgerechten Schmierstoffmenge bei der Minimalmengenschmierung (MMS) im Projekt InPro-MMS - gefördert vom SMWK im Rahmen der Forschungsförderung an Fachhochschulen 2013 - erbracht werden. Aktuell erfolgt die Festlegung der anzuwendenden Schmierstoffmenge bei der MMS-Bearbeitung erfahrungsbasiert. Pauschal werden Volumenströme von 30 – 50 ml/h je Maschine gewählt, ohne die tatsächlich notwendige Menge je Bearbeitungsfall zu kennen. Ausgangspunkt für das Projektvorhaben waren eigene Voruntersuchungen an der WHZ, in denen das Einsparpotenzial, welches sich aus einer gezielten Mengenreduktion ergibt, aufgezeigt werden konnte.
Aufgabe
Zur zielgerichteten MMS-Mengenreduktion ist es erforderlich, Bearbeitungsaufgaben bei den industriellen Partnern zu analysieren, eine begründete Werkstoffgruppenbildung vorzunehmen und gruppenspezifisch, im Spanungslabor der WHZ, die tatsächlich erforderlichen MMS-Mengen zu ermitteln. Thermografische Untersuchungen werden begleitend durchgeführt, um MMS-bedingte Verschleißeffekte zu erklären. Weiterhin ist eine geeignete Kenngröße abzuleiten, mit deren Hilfe die werkstoffgruppenspezifische Vorausberechnung der erforderlichen MMS-Menge, bei unterschiedlichen Spanungsbedingungen, möglich wird.
Ergebnis
Basierend auf den Analysedaten zu typischen MMS-Bearbeitungsaufgaben, wird ein neuer Ansatz zur Werkstoffgruppenbildung erarbeitet (Gleichung 1). Ziel ist die Gruppierung typischer Werkstoffe in einer möglichst kleinen Gruppenanzahl, mit jeweils gleichem MMS-Bedarf. Grundlage des neuartigen Ansatzes GB (Gruppenbildner), stel-len dabei verfügbare bzw. leicht zu ermittelnde Werkstoffkennwerte (kc1.1, lambda) dar.
GB = kc1.1/λ (1)
Neben dem Nachweis der Eignung von GB (Gleichung 1) zur Werkstoffgruppenbildung, sind experimentelle Untersuchungen zur Ermittlung des tatsächlich erforderlichen MMS-Bedarfs beim Stirn-Planfräsen an verschiedenen, vorausgewählten Werkstoffen, unter Variation des MMS-Volumenstroms und der Spanungsbedingungen (bspw. vc), durch-zuführen. Bild 1 zeigt hierzu beispielhaft die Ergebnisse am Vergütungsstahl 42CrMo4.
Die Ergebnisse verdeutlichen unmittelbar, dass die heute üblichen Volumenströme von 30 – 50 ml/h, wesentlich zu hoch bemessen sind. Am Werkstoff 42CrMo4 führt die Volumenstromreduktion um den Faktor 10 (50 ml/h auf 5 ml/h) zu einer Zunahme der Standzeit (Senkung werkzeugabhängiger Kosten), wobei dies gleichzeitig mit einer erheblichen Reduktion der Emissionen in den Fertigungsstätten einhergeht. Die Variation der Schnittgeschwindigkeit vc – im technisch sinnvollen Rahmen – hat dabei keinen Einfluss auf den optimalen MMS-Volumenstrom.
Die begleitende thermische Analyse des Spanungsprozesses zeigt – ausgehend von der Trockenbearbeitung (0 ml/h) – den typischen Abfall der Spantemperatur durch den Einsatz der MMS-Technik. Die dann ermittelten Standzeitmaxima T je Versuchswerkstoff, befinden sich größtenteils im Bereich von 5 – 10 ml/h, dem Bereich der größten Temperaturänderung gegenüber der Trockenbearbeitung.
Die Projektergebnisse stellen die Basis für den zukünftig kosten- und umweltschonenden Einsatz der MMS-Technik dar. Gezielte, werkstoffspezifische MMS-Mengenreduktionen führen zu direkten Kosteneinsparungen (werkzeugabhängige Kosten, Schmierstoffkosten, usw.) und gleichzeitig zur Steigerung des Arbeits- und Gesundheitsschutzes infolge reduzierter Emissionen in den Fertigungsstätten.
Weiterführende Betrachtungen zur Verbesserung der Werkstoffgruppenbildung sowie zu anderen Fertigungsverfahren und Werkstoffen, sind im Rahmen eines Folgeprojektes geplant.

Standzeit T in Abhängigkeit von MMS-Volumenstrom V ̇ und Schnittgeschwindigkeit vc /IfP/
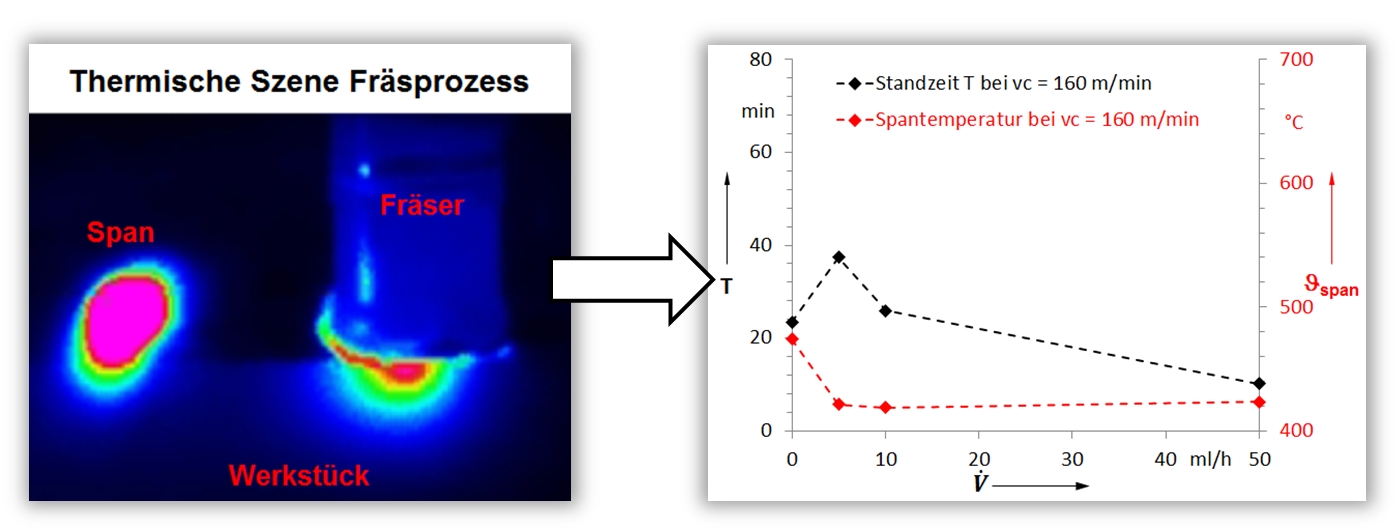
Thermische Szene des Fräsprozesses sowie Standzeit T und Spantemperatur Span in Abhängigkeit des MMS-Volumenstroms V ̇ (Bsp. Warmarbeitsstahl 55NiCrMoV6) /IfP/
Anhang
Bild : Standzeit T in Abhängigkeit von MMS-Volumenstrom V ̇ und Schnittgeschwindigkeit vc /IfP/

Bild : Thermische Szene des Fräsprozesses sowie Standzeit T und Spantemperatur Span in Abhängigkeit des MMS-Volumenstroms V ̇ (Bsp. Warmarbeitsstahl 55NiCrMoV6) /IfP/
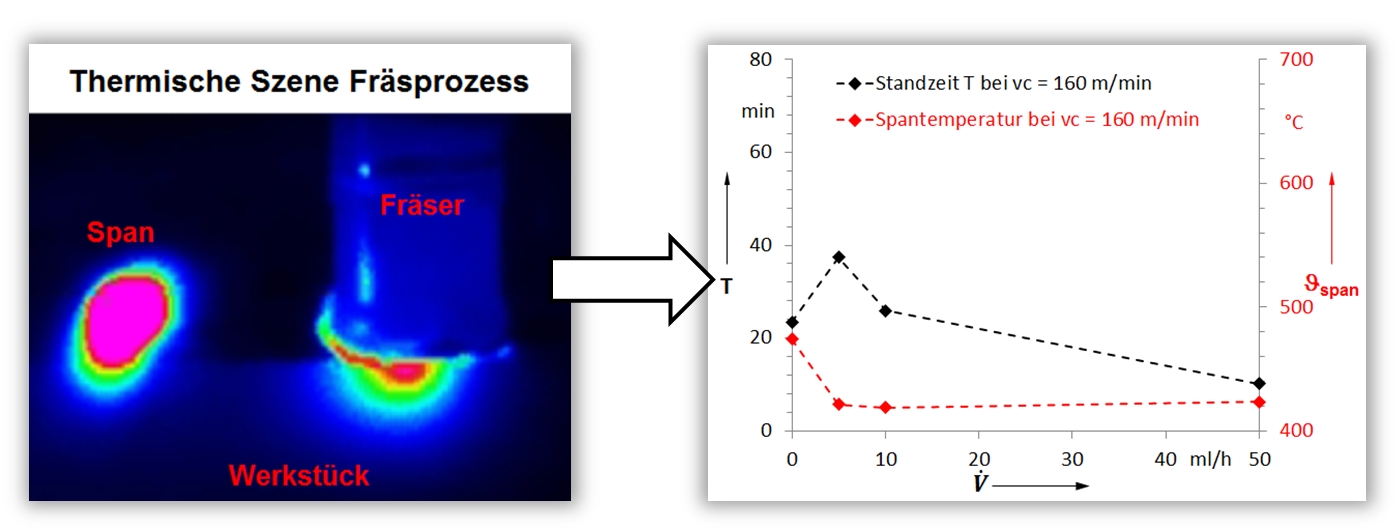